How Strain Gauges Deliver Reliable Measurements Under Pressure
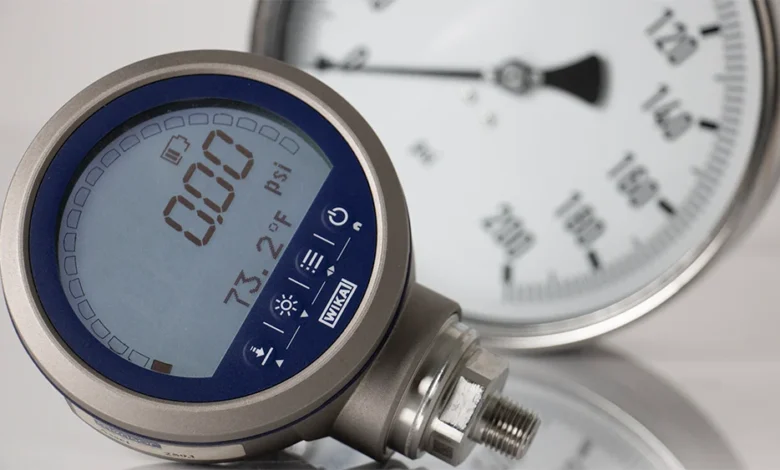
In the critical fields of engineering, manufacturing, and scientific research, the accuracy and reliability of measurements are non-negotiable. Strain gauges, with their ability to detect even the slightest changes in material deformation, stand as pivotal tools in ensuring these precise measurements. Their application in various industries underlines the trust placed in their capability to provide dependable data.
Find below five key aspects that highlight how strain gauges manage to offer such dependable and accurate measurement solutions.
High sensitivity to deformation
Strain gauges are designed with materials that exhibit significant changes in electrical resistance when stretched or compressed. This sensitivity allows them to detect minute deformations in the substrate they are attached to, providing an accurate measure of strain. The gauge factor, a key specification of strain gauges, quantifies this sensitivity, ensuring that measurements are both reliable and reproducible across various applications.
Versatile application methods
The effectiveness of strain gauges is partly due to the versatility in their application methods. They can be bonded to almost any material, including metal, plastic, and concrete, allowing them to measure strain in a wide range of structural, mechanical, and electronic components. This adaptability ensures that strain gauges can provide accurate measurements in diverse environments and conditions.
Advanced signal processing
Modern strain gauges are often part of sophisticated measurement systems that include advanced signal processing capabilities. These systems amplify and convert the electrical signals from the strain gauges into digital data that can be accurately analyzed. The use of such technology minimizes noise and errors, enhancing the dependability of the measurements.
Temperature compensation
Temperature changes can affect the physical properties of materials, including their electrical resistance. Strain gauges are designed with temperature compensation features that adjust for these changes, ensuring that the measurements reflect only the strain caused by mechanical forces, not temperature fluctuations. This is crucial for maintaining accuracy in environments where temperature varies.
Calibration and standards compliance
Finally, the reliability of strain gauges is ensured through rigorous calibration against known standards. Manufacturers and users often adhere to international standards, which dictate the calibration procedures and performance criteria for strain gauges. This adherence to standards guarantees that the measurements are accurate and consistent, meeting the stringent requirements of professional and research applications.
Final thoughts
Strain gauges embody the essence of precision measurement, providing industries and researchers with the tools they need to assess material performance under stress accurately. Strain gauges offer a reliable way to gather critical data, ensuring the safety, efficiency, and innovation of engineering solutions.